Dal cartone al gesso: l’architetto in 3D ritrova le linee impossibili
Davide Tresoldi e Francesco Aiello, di FormA.3. hanno trovato nella stampa a gesso la formula perfetta per riprodurre il centro radiografico studiato per far sognare Algeri. «Linee e incastri perfetti, chi guarda il progetto può vedere l’originale»
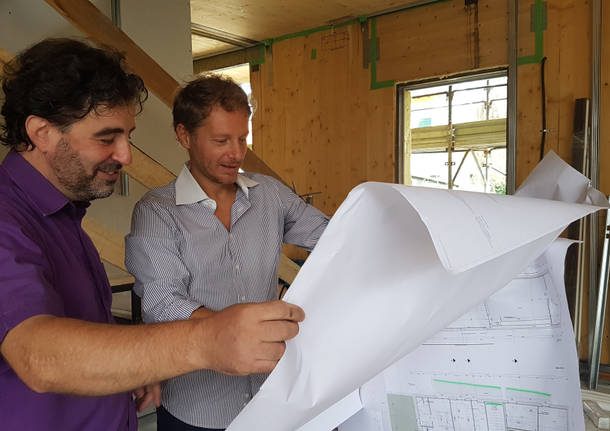
Il cartone piace ancora, ma vuoi mettere il gesso? Due architetti (Davide Tresoldi di 41 anni e Francesco Aiello di 50), il loro progetto per un centro radiografico in Algeri, la riscoperta delle forme tradizionali arabe, il gusto e lo stile per qualcosa di diverso e un’infinita passione per il legno (perché offre prestazioni migliori e garanzie più elevate di durabilità rispetto all’edilizia tradizionale). Poi, Faberlab.
Il discorso con i due soci di “FormA.3.” (Form sta per forma, A per Aiello e 3 per Tresoldi), studio associato con base a Giussano (provincia di Monza Brianza) inizia con un’ammissione di colpa: «È vero, non conoscevamo la stampante 3D a polvere di gesso. Sapevamo, invece, del 3D con l’uso di filamenti plastici poco adatti però a superare le complessità tecniche del progetto algerino – dichiara Francesco Aiello – Allora abbiamo ceduto alla curiosità, e se in un primo momento la stampante in gesso non era nei nostri pensieri, poi è diventata indispensabile per sviluppare al meglio la superficie della parete del centro radiografico».
La prima difficoltà è stata proprio quella: «Si tratta di una specie di scultura con linee molto mosse e una serie di triangoli che poggiano su diversi piani con rientri e sbalzi. Una parete traforata con motivi arabi che garantisce la luminosità degli ambienti e una quinta posta sul davanti che fa da frangisole: la luce illumina ma se ne controlla l’intensità. Insomma niente che somigli alla solita facciata a vetri. Così è l’intero edificio con laboratori, camminamenti e uffici che da questa gestione della luce aumentano il confort per i pazienti. Anche se non si tratta di una residenza, perché qui le persone ci devono passare poco tempo, abbiamo puntato al loro completo benessere: anche la terrazza all’ultimo piano, dedicata al personale che ci lavorerà, è adatta ad un momento di grande relax perché anche lì abbiamo introdotto un effetto ombreggiante che fa stare bene».
Con un modellino in cartone, il committente avrebbe percepito ben poco del valore di questo progetto. E qui entra in gioco la stampante a polvere di gesso: «Per poter esprimere tutta la complessità del nostro lavoro, il gioco delle linee e i loro incastri serviva una macchina precisa. In caso contrario avremmo dovuto lavorare con le stampanti più tradizionali con FDM, realizzare ogni singolo triangolo della facciata e assemblarli a mano. No, non faceva al caso nostro. Con la stampante a gesso abbiamo scoperto che non ci sarebbero stati limiti nel presentare il progetto in tutte le sue più piccole definizioni. E il bello è che in Faberlab abbiamo trovato una guida ideale. Un valido alleato, perché sono stati i ragazzi di questo laboratorio digitale a consigliarci nei metodi migliori per esprimere il nostro pensiero».
Risultato? Il gesso ha una resa formidabile e quello che hanno fatto Aiello e Tresoldi ha soddisfatto tutti. A tal punto che si è stampato l’intero edificio e, una volta raggiunta Algeri, il modellino si è rivelato la famosa «ciliegina sulla torta. Se non avessimo presentato il progetto in 3D con la pulizia di tutti quei dettagli – prosegue Aiello – probabilmente ci avrebbero rimandato a casa. Tutto è stato più facile: il modellino è scenografico e il bianco risalta in modo spettacolare la creatività del lavoro dell’architetto».
Il modo di lavorare cambia, per tutti. Per le imprese e per i liberi professionisti. La nuova frontiera della stampa 3D non solo è consolidata ma compie passi da gigante perché «queste macchine ci permettono di esprimere in modo compiuto la nostra fantasia. Ora, con risultati soddisfacenti, possiamo realizzare progetti molto complessi. Se prima il rendering era considerato uno strumento all’avanguardia, ora potrebbe rivelarsi un limite perché sul cliente non ha lo stesso impatto di un modello in 3D e non porta allo stesso coinvolgimento. Il modellino di Algeri si può toccare con mano e, di certo, per progetti di questa importanza utilizzeremo ancora la stampante a polvere di gesso. I tempi di realizzazione di un modello sono rapidissimi: quello del centro radiografico ci è stato consegnato in soli due giorni». I vecchi plastici vanno in soffitta? «Il plastico richiede molto più tempo. Da parte nostra, magari anche solo per studiare quello che dovremo fare dopo, continueremo a realizzarli». Rigorosamente in cartone.
TAG ARTICOLO
La community di VareseNews
Loro ne fanno già parte
Ultimi commenti
Felice su Vita, carriera e famiglia: Rocco Siffredi si racconta sul palco di Varese fra sorrisi e lacrime
Alessandra Toni su Max Felicitas a Gallarate incatenato fuori dall'Isis Ponti: “Libertà, libertà"
Felice su Gli studenti dell'istituto Ponti di Gallarate determinati a incontrare Max Felicitas anche fuori dalla scuola
rosa su Max Felicitas a Gallarate incatenato fuori dall'Isis Ponti: “Libertà, libertà"
Felice su La guerra in Ucraina e la sfida dell'occidente: servono disciplina, determinazione e pragmatismo
lenny54 su La guerra in Ucraina e la sfida dell'occidente: servono disciplina, determinazione e pragmatismo
Accedi o registrati per commentare questo articolo.
L'email è richiesta ma non verrà mostrata ai visitatori. Il contenuto di questo commento esprime il pensiero dell'autore e non rappresenta la linea editoriale di VareseNews.it, che rimane autonoma e indipendente. I messaggi inclusi nei commenti non sono testi giornalistici, ma post inviati dai singoli lettori che possono essere automaticamente pubblicati senza filtro preventivo. I commenti che includano uno o più link a siti esterni verranno rimossi in automatico dal sistema.